Why Prism RMC’S Ready-Mixed Concrete is better than
Site Mixed Concrete
While site-mixed concrete might seem cost-effective at first glance, it often leads to a host of problems during and after construction. The process of mixing concrete on-site can introduce inconsistencies in the mixture, resulting in poor quality or compromised structural integrity. Delays in mixing and pouring can also disrupt project timelines and increase labour costs. Additionally, the lack of precise measurements and control over the mixing process might lead to material wastage or higher long-term expenses due to repairs and maintenance.
Prism RMC offers a dependable alternative with its high-quality ready-mixed concrete, ensuring on-time delivery and expert guidance. Our ready-mixed concrete is produced in a controlled environment, guaranteeing consistent quality and strength for every batch. This not only enhances the durability of your structures but also reduces the risk of future complications.
Benefits of Choosing Prism RMC:
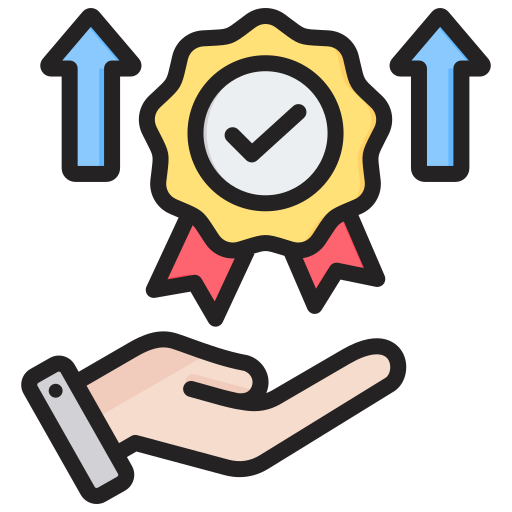
Consistent quality
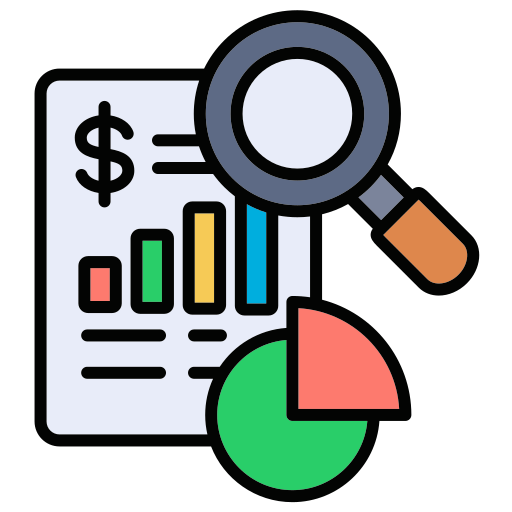
Higher transparency
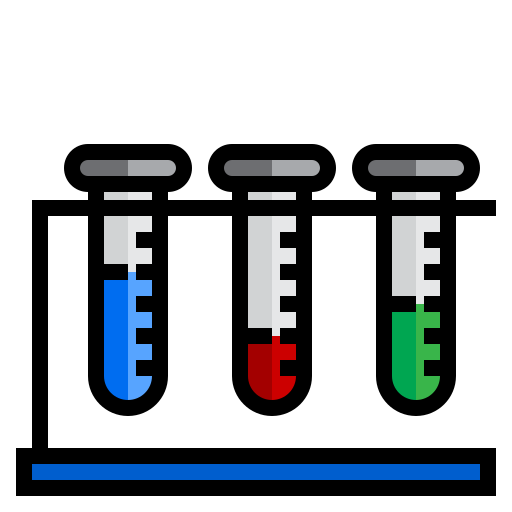
Sampling and testing
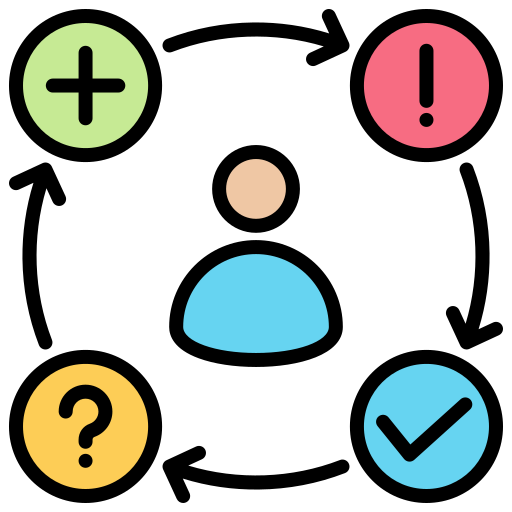
Extended service life of the strucstructure
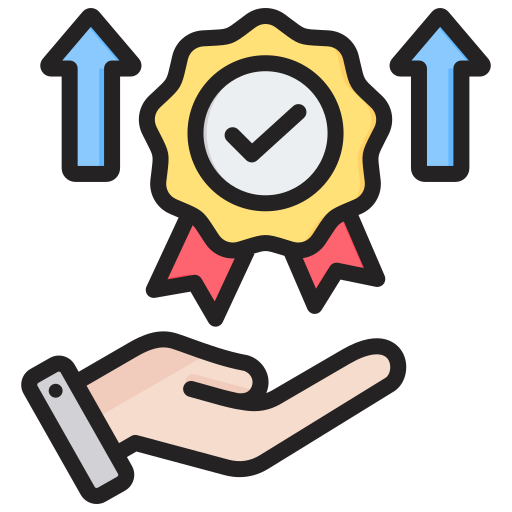
Excellence quality and durability
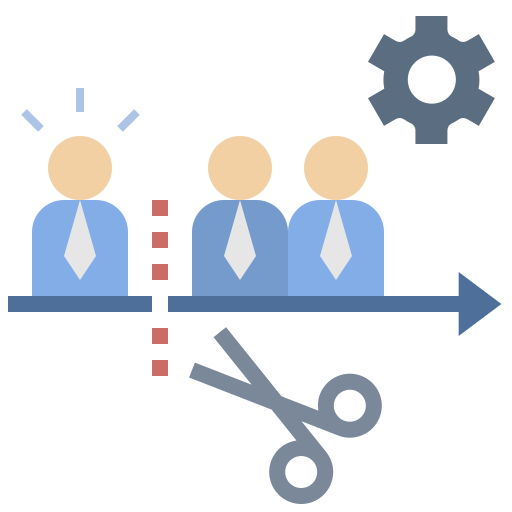
Reduced labour requirement at site
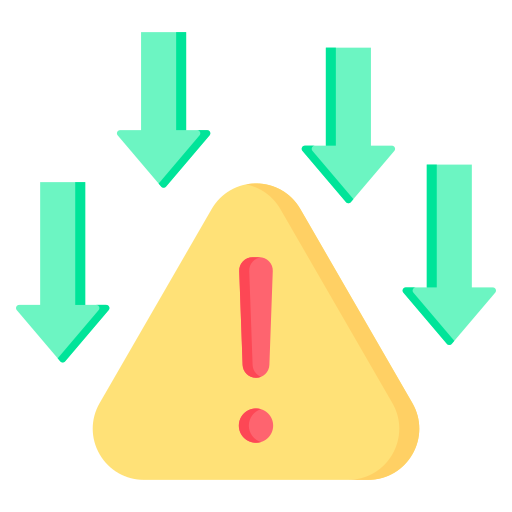
Reduced chances of damage to your reinforcement
Site-Mixed Concrete
- Inconsistent mixing in a small mixer.
- Cement and aggregates are stored in the open.
- It is difficult to maintain raw material proportions batch-wise. Moreover, there is no traceability.
- Manual and erratic addition of water leads to poor quality of concrete.
- Unregistered and unorganized operators.
Prism RMC’S Ready Mixed Concrete
- Consistent mixing in high speed pan or turbo shaft mixer.
- Cement stored in watertight silos and aggregates in enclosed bins.
- Correct proportioning of raw materials though fully computerized batching plants that even store the batched data.
- Accurately batched water helps to maintain quality and durability.
Laborious and time consuming: slab casting by human chain
- Labour intensive.
- Slow progress.
Efficient and fast slab casting using a concrete pump
- Less labour required; entire operation carried out in a safe and efficient manner.
- Ensures speed of construction.
No check / testing of incoming raw materials
- Untested aggregate results in improper grading and quality.
- Aggregate is dumped along the roadside.
- Intermixing of the aggregate with each other occurs, along with debris from the road.
- Poor quality aggregate culminates in bad quality concrete, leading to higher life cycle costs.
- Creates dust and mess all around the site.
Raw materials are checked before entry into the plant
- Aggregate of unacceptable grading / quality is rejected.
- Aggregate is stacked in a proper ground storage bays.
- This prevents inter mixing and also keeps the aggregate under shade.
- Concrete made from such aggregate conforms to the quality norms.
- Good housekeeping possible at the site.